Film faced plywood is a material widely used in the fields of construction and decoration. Vietnamese film faced plywood products are increasingly developing and asserting their quality in the Global market. So, what exactly is this material? What are its practical applications in construction projects? And what factors need to be considered before purchasing? This article will provide a comprehensive overview of this versatile material.
Contents
Film Faced Plywood: Nature and Structure
Basically, this is a type of industrial plywood covered with a phenolic or melamine film on both surfaces. This coating not only provides an aesthetic appearance but also plays a crucial role in protecting the inner wood layers from negative environmental impacts such as humidity, water, chemicals, and abrasion.
The structure of this type of plywood typically consists of multiple thin layers of natural wood (veneer) pressed tightly together under high temperature and pressure, using specialized adhesives such as WBP (Water Boiled Proof) with absolute water resistance. The outer film layer is tightly bonded to the plywood surface, forming a unified whole, enhancing the product’s durability and lifespan. Common types of wood used for the veneer include hardwood, mixed forest wood, or a combination thereof, depending on the requirements for durability and cost.
Outstanding Features of Film Faced Plywood
The reason this material is widely applied in construction is due to its following outstanding features:
- Superior Water Resistance: The film coating and WBP glue give the plywood absolute water resistance, preventing deformation, blistering, or decay in humid environments.
- Smooth Surface, Abrasion and Chemical Resistance: The film coating creates a smooth, flat surface, which helps the concrete surface after pouring to be beautifully finished and resistant to corrosion from some common chemicals.
- High Mechanical Strength: The multi-layer pressed wood structure gives this material good bending strength, stiffness, and load-bearing capacity.
- Easy to Work With and Cut: This material is lightweight compared to other traditional materials, making it easy to transport, install, and cut according to project requirements.
- Aesthetics: The film surface comes in various colors and wood grain patterns, meeting aesthetic requirements for some special applications.
- Reusability: Especially in concrete formwork applications, high-quality film faced plywood can be reused many times, providing high economic efficiency.
- Environmentally Friendly (depending on the type): Produced from sustainable wood sources and using low-formaldehyde adhesives.
Diverse Applications of Film Faced Plywood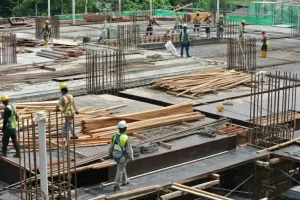
With the above outstanding features, this material is widely applied in various fields of the construction and interior design industries:
-
Concrete Formwork: This is the most common application. Thanks to its load-bearing capacity, water resistance, and smooth surface, it is used to create molds for concrete structures such as columns, beams, floors, walls, and foundations.
-
Flooring: With its resistance to moisture and abrasion, some special types of film faced plywood are used as flooring for areas with high humidity or high traffic.
-
Partitions: The aesthetic appeal and moisture resistance make it an ideal material for both indoor and outdoor partitions.
-
Container and Truck Body Manufacturing: Its high mechanical strength and resistance to harsh weather conditions make it a suitable material for manufacturing containers and truck bodies.
Things to Know Before Buying Film Faced Plywood
Choosing the right type of film faced plywood for the intended use is extremely important to ensure project efficiency and optimize costs. Here are some factors you need to carefully consider before making a purchase decision:
- Type of Film Coating: Phenolic film coatings generally have higher durability and better resistance to scratches and chemicals compared to melamine film coatings. However, the cost of phenolic film faced plywood is also higher.
- Quality of Veneer and Core Wood: The quality of the inner veneers and the type of wood used for the core will directly affect the mechanical strength, load-bearing capacity, and lifespan of the product. Plywood with a hardwood core usually has better stability and load-bearing capacity. Ask the supplier to provide detailed information about the origin and quality of the wood.
- Type of Adhesive Used: WBP glue is the top choice for applications requiring high water resistance, especially in construction. Other types of glue may be cheaper but may not guarantee the same level of durability and moisture resistance.
- Thickness and Dimensions: This material comes in various thicknesses and dimensions. Choosing the right thickness and dimensions will help optimize material usage and minimize waste during construction.
- Number of Reuses: This is an important factor in evaluating the quality of Film Faced Plywood. High-quality film faced plywood can be reused multiple times if properly stored.
- Supplier Reputation: Choosing a reputable supplier is key to ensuring you purchase quality products at a reasonable price with good after-sales service. Thoroughly research the supplier’s experience, quality certifications, and feedback from previous customer
Finding a Reputable Plywood Supplier in Vietnam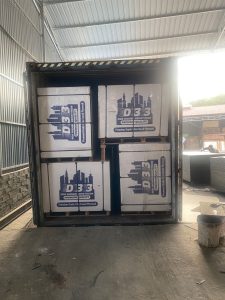
If you are looking for a supplier of good quality film faced plywood in Vietnam, Global Dream Co., Ltd. is a top choice. Global Dream provides stable quality products that meet the stringent standards of both domestic and international markets.
Global Dream’s products stand out with their durable veneer bonding, perfect resistance to delamination, and absolutely secure veneer adhesion. Global Dream’s products are currently exported to many demanding markets worldwide.
Specific Technical Specifications of Global Dream:
- Core Wood: Eucalyptus, Acacia, Local Plantation Hardwood…
- Surface: Phenolic Film
- Finished Product Dimensions: 1220 x 2440mm, 1250 x 2500mm
- Adhesive: Water Boiled Proof (WBP) Glue: Melamine 7%-25%
- Tolerance: ± 0.3 – 0.5mm
- Maximum Moisture Content: 12%
- Thickness: 10mm-27mm (12mm, 15mm, 18mm, 21mm, 24mm, and 27mm…)
- Number of Reuses: Up to 25 times (if used and stored properly)
With a variety of sizes and the ability to customize the core wood according to requirements, Global Dream is committed to providing customers with the most suitable products for each project.
Please contact us for free consultation and ordering.
Sincerely
https://plywoodvn.com/what-is-bintangor-plywood-good-quality-plywood/